|
Electropolishing,
Passivating,
Cleanroom
Packaging,
Tube EP (ID/OD) |
|
714-434-6604 |
|
Electropolishing is
an electrochemical
process that yields
a bright, smooth,
non-corroding,
super-clean finish. |
|
EP offers tremendous
benefits in many
applications:
Deburrs all edges,
leaving smooth
surfaces. Uniformly
removes molecular
impurities, leaving
a chromium-rich, non-corroding finish.
Reduces friction and
galling and extends the
fatigue life of many
machined and cast
parts. Micro-sizes
stainless steel
parts, allowing
ultra-precise
component fitting. |
|
Electropolishing
Process |
|
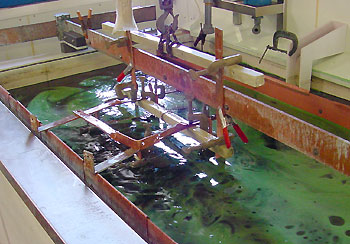 |
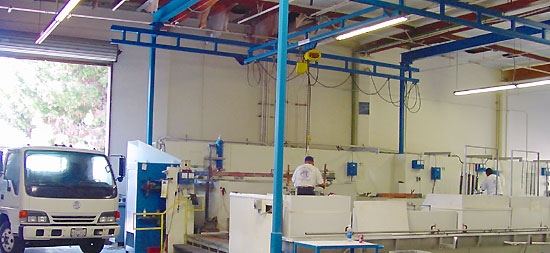 |
We process all kinds
of stainless steel,
as well as titanium,
inconel, and other
alloys. |
|
10,000 Square Foot
Production Facility |
|
Common Applications
for Electropolishing: |
Industries:
semiconductor,
aerospace,
laboratory,
automotive, food and
beverage processing,
pharmaceuticals,
medical/dental,
petrochemical |
Components: marine,
machined parts,
casting, stamped
parts, sheet metal,
tubes, fittings,
weldments, wire
products, frames,
tanks, more. |
|
Our extensive
experience in
cleanroom-compatible
manufacturing helps
us meet the most
demanding
cleanliness
standards.
Ultra-smooth
electropolished
stainless steel
bench tips, frames,
wire shelving,
storage enclosures,
and other cleanroom
furnishings wipe
down clean and will
not shed
contaminants. |
|
Cleanroom Compatible
Manufacturing |
|
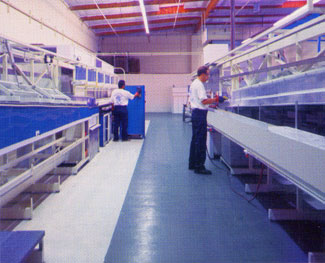 |
Electropolishing
An anodic dissolution
of metals is the basic
mechanism for the
electropolishing of metals.
The component to be
electropolished is connected
to the positive end of a DC
power supply while the
negative lead is connected
to cathode plates or
matching tooling. The
assembly is submerged in an
electrolyte and current is
allowed to flow, The actual
process consists of an
accelerated corrosion step
that is controlled to obtain
desired effects. |
|
Passivation
The current approach
to passivation is to
complete the cleaning of the
stainless components by
doing the passivation step
with nitric acid or citric
acid; either step shall be
in conformance to ASTM A967,
QQ-P-35, MIL-S-5002.
Nitric Acid: is used in
completing the passivation
of machined components and
in post electropolishing
operations. This step
provides an effective means
of removing all free iron
from the surface of the
finished part. The chemistry
of the surface will be free
of iron and all acid soluble
impurities will be removed. |
|
Citric
Acid
Used as an
alternative nitric acid, or
in combination with nitric
acid. Citric acid based
chellation baths are used in
a three step process to
remove all impurities and to
provide a surface that is
compatible with biomedical
applications. |
|
Cleaned for O2 Service
Oxygen service
applications require that
all components be free of
organic residue and be in
compliance with the
specified standards. We can
provide components per
designation: G93-96.
Standard practice for
cleaning methods and
cleanliness levels for
materials and equipment used
in oxygen-enriched
environments. |
|
|
|
E-MAIL:
albert@atep.com |
Alloy Tech Electropolishing |
2220 South Huron Drive, Santa Ana, CA 92704 |
714-434-6604 |
FAX 714-434-6646 |
|
©2022 Alloy Tech Electropolishing, Inc. All rights reserved. Website
hosting:
PerfectNet.com |
|
|
|
|